Flooring Guide
Blue Ribbon Flooring Co, Inc.
Understanding Hardwood Floor Grades
Hardwood floor grades lack a universal standard enforced by a governing body. Instead, grading systems are typically established by individual manufacturers and suppliers, each using their criteria to evaluate the wood's appearance and quality.
- Industry organizations like the
National Wood Flooring Association (NWFA) provide helpful guidelines for hardwood grading. The NWFA’s technical manual outlines grading criteria for both domestic and imported hardwoods, offering a valuable reference for manufacturers and suppliers.
Blue Ribbon Flooring's Wood Flooring Guide
Hardwood flooring is graded based on its appearance, including natural imperfections like knots, streaks, and color variations.
Red & White Oak Grades
- Clear Wood: Minimal character marks, creating a smooth and uniform look.
- Select Wood: Natural color variations with small knots and streaks for subtle character.
- Common Wood (No. 1 and No. 2): Features prominent knots, streaks, and color variations for a rustic look.
- No. 1 Common: A blend of light and dark tones with visible character marks.
- No. 2 Common/Character: Rustic with prominent natural features for a bold, unique aesthetic.
- Live Sawn White Oak: Natural grade, allowing for large sound knots, prominent color variations, along with varying wood characteristics. Will admit the following: Open knots, open characters, (up to 1’’ in diameter) splits ¼’’ wide, that can be filled or defected out on the job site. Unlimited, worm holes, checks, streaks, and sapwood.
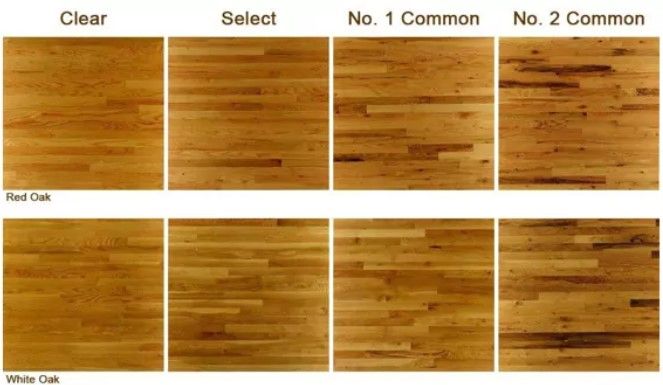
Hickory Grades
- Clear Wood: Natural variations in heartwood and sapwood coloration, along with some allowable natural wood characters. Will admit the following: Occasional pin knots (1/4’’ in diameter), small burls, streaks.
- Character Grade: Distinct natural variations in heartwood and sapwood coloration, along with varying natural wood characters and sound knots. Will admit the following: Open knots and open characters (up to ½’’ in diameter that are fillable) worm holes, checks, streaks, bird pecks. Unlimited heartwood/sapwood.
Beech, Birch, and Hard Maple Grades
- First Grade: High durability with minimal imperfections and natural color variations.
- Second Grade: Includes streaks, sound knots, and checks while maintaining serviceability.
- Third Grade: Allows for more imperfections, suitable for functional and rustic floors.
By understanding these common terms and the flexibility within grading systems, you’ll be well-equipped to select the hardwood flooring that best suits your style and needs.
Different Types of Lumber Cuts
Milling refers to how a manufacturer divides a log into floorboards. This process impacts its structure and appearance, especially its grain. There are four main types of milling to choose from - live, plain, rift, and quarter. To help you choose which option is right for you, check out this guide to the different types of lumber cuts.
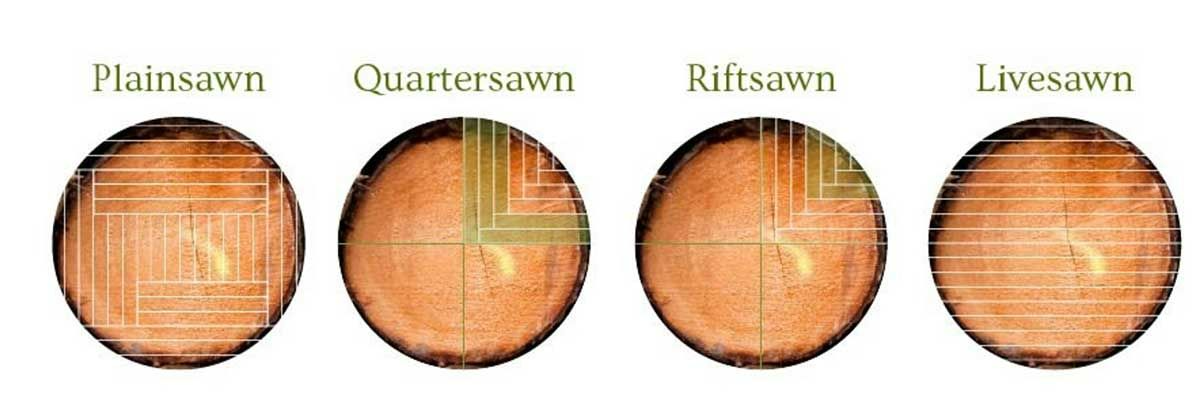
Solid Hardwood vs. Engineered Hardwood
Solid Hardwood:
- Made from a single piece of 100% hardwood.
- Offers timeless beauty, exceptional durability, and the ability to be refinished multiple times.
- Best for above-ground spaces like living rooms, dining rooms, and bedrooms.
Engineered Hardwood:
- Constructed with a real wood top layer, wood bottom, and a crisscrossed plywood core for stability.
- Performs well in areas prone to temperature and humidity changes, like basements or over radiant heating.
Durability and Sound:
- Solid hardwood has a robust feel underfoot and can last decades.
- Engineered hardwood is also durable, though its refinishing potential depends on the thickness of the top layer.
Cost:
- Solid hardwood is often pricier due to its longevity and natural beauty, while engineered hardwood provides budget-friendly options without sacrificing style.
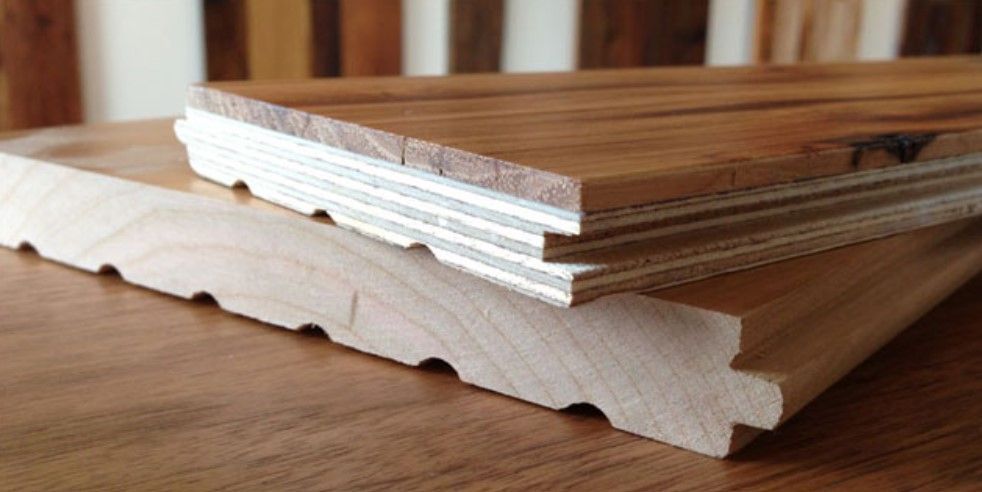
Luxury Vinyl Plank (LVP)
Luxury Vinyl Plank (LVP) has emerged as a stylish, durable, and cost-effective alternative to traditional hardwood flooring. Blue Ribbon Flooring stocks four premium styles of LVP and offers custom order options from other leading brands.
- SPC: Stone Plastic Composite LVP, also known as rigid core, is the toughest and most durable vinyl product on the market. It is known to hold up well in high traffic areas.
- WPC: Wood Plastic Composite LVP has a core made of recycled wood pulp and plastic composites. The core is enhanced with a foaming agent, making it slightly softer and adding additional comfort underfoot.
Share On: